Construction d'un navire : le bon choix du matériau
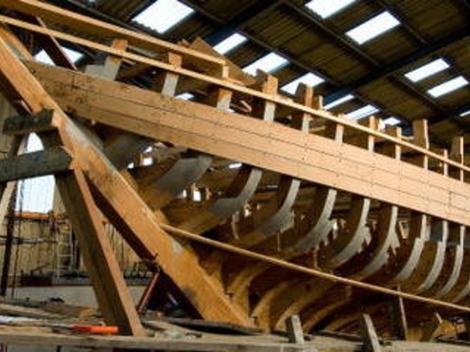
Depuis le tronc d'arbre flotté, pirogue originelle, qui fut peu à peu creusé pour en améliorer la masse, la stabilité et la capacité de charge, l'être humain a patiemment peaufiné et amélioré son savoir faire et sa connaissance des matériaux, ceci dans plusieurs buts.
Tout d'abord, pouvoir construire un bateau sans être limité par les dimensions des arbres ou autres végétaux disponibles (roseaux, bambous...). Imaginez la taille de l'arbre nécessaire pour y creuser la Recouvrance d'un seul tenant ! Il a donc fallu apprendre à débiter des planches, puis soit les ajouter en haut du tronc d'arbre, pour en augmenter le franc bord (utilisation 'hauturière'), soit de les intercaler au milieu du tronc scindé en deux, pour en augmenter la largeur (utilisation lacustre).
Ce faisant, il a donc été nécessaire de trouver un moyen d'étanchéifier les jonctions entre plusieurs éléments, afin de conserver une coque la plus intègre possible: On peut citer les techniques de calfatage, de bordage à clin, l'enduction de brai, mais aussi l'entoilage garni de bouses animales !
Une autre nécessité est également celle de la solidité, conjuguée à la légèreté. Quel que soit le matériau utilisé, plus on souhaite que l'ensemble de la coque soit rigide (à masse égale), ou léger (à résistance égale) plus il est nécessaire d'ajouter au creux de notre enveloppe étanche (le bordé) un moyen de rigidifier celui ci.
C'est ainsi que l'on est arrivé aux structures, semblables aux ramifications d'une feuille ou à un squelette animal, qui ont été employées pendant des siècles sur les navires en bois. Une colonne vertébrale (la quille) supporte des ramifications transversales (les varangues et membrures).
Avec l'avènement de l'acier, l'organisation structurelle des navires a pu évoluer. Il est donc devenu possible de la concevoir de manière a intégrer des renforts et des raidisseurs spécifiques aux besoins structurels. Cette évolution s'est encore plus marquée au 20eme siècle, avec l'apparition de matériaux performants tels que le contreplaqué, l'aluminium, et les matériaux composites. La structure de certains navires de plaisance s'en est d'ailleurs grandement simplifiée.
Dans la construction navale de plaisance, après la période faste du contreplaqué, on utilise a très grande échelle un mode constructif permettant de s'affranchir de nombreuses contraintes de forme : le composite fibre de verre / résine polyester. Ce matériau présente l'intérêt d'un très faible coût, et d'une reproductibilité aisée en grande série, grâce aux techniques de moulage. En contrepartie, c'est un composite relativement peu résistant, il induit donc des bateaux assez lourds, ou aux bordés souples (cf quarter tonners des années 70/80), et il est sujet à l'osmose.
En utilisant ce matériau non plus en tant que peau épaisse (monolithique), mais sous forme de sandwich, la problématique du rapport poids/rigidité est moins prégnante. En revanche, il est nécessaire d'apporter une attention toute particulière au matériau d'âme incorporé entre les deux peaux de fibre de verre. Le balsa, bois naturellement léger et très résistant à la compression, ne supporte pas l'eau. Il est donc indispensable de se prémunir de toute infiltration, sous peine de voir notre sandwich se délaminer au fil des ans. Les mousses polymères quand à elles craignent moins l'humidité (PVC, PET).
La fibre de verre est certes bon marché, mais ses caractéristiques mécaniques peu élevées, de même que sa densité importante (2600kg/m³), la rendent beaucoup moins intéressante pour des applications dites de "performance". Les fibre aramides (Kevlar) à la densité très faible (1400kg/m³) ont été un temps utilisées, notamment sur les VOR60. Mais la généralisation du carbone, ainsi que la complexité de mise en œuvre du kevlar, l'ont rapidement fait disparaître de la plupart des bateaux de course. Ils sont aujourd'hui pour la plupart construit en fibre de carbone (densité 1800 kg/m³), associé à des âmes en mousse (PVC ou SAN) ou en nid d'abeille (nomex). Quelques jauges en interdisent ou restreignent l'usage, afin de contenir les coûts (Mini de série, Class 40, Multi 50).
Alors que la fibre de verre s’accommode très ben d'être stratifiée avec de la résine polyester, les autres fibres se travaillent avec de la résine epoxy, plus coûteuse, mais aux propriétés mécaniques de loin supérieures. L'époxy est également insensible à l'osmose. En revanche, il est nécessaire pour sa mise en œuvre de respecter rigoureusement des conditions minimales de température et d'hygrométrie.
Qu'ils soient à base de fibre de verre, de carbone, d'aramide ou de dyneema, tous ces composites utilisant des résine thermodurcissables posent un gros problème écologique. La production de matière première se base sur des dérivés du pétrole, la mise en œuvre dégage des vapeurs et solvants toxiques et cancérigènes, et leur recyclage est quasiment impossible.
Si les techniques de mise en œuvre ont évolué, de manière à protéger plus les opérateurs et limiter le rejet de composés volatils, tout en augmentant la qualité du produit fini, les matériaux de base restent toujours aussi peu écologiques. Des expérimentations sont aujourd'hui en cours, afin de développer l'usage des fibre naturelles en lieu et place de la fibre de verre, ainsi que pour intégrer une proportion non négligeable de matière organique naturelle dans la formulation des résines.
Le contreplaqué, quant à lui, associe d'intéressantes propriétés mécaniques, une faible densité, ainsi qu'un impact écologique moindre. Si sa mise en œuvre nécessite toujours l'utilisation de résines (autrefois phénoliques, aujourd'hui époxy) ainsi que des renforts en fibre de verre ou de carbone, un bateau construit en contreplaqué reste consititué à plus de 60% de matière naturelle. En contrepartie de ses multiples qualités, le contreplaqué impose l'utilisation des formes développables, qui ont donné aux Corsaire, Muscadet, et autres Vaurien leurs carènes anguleuses tant décriées à leurs débuts.
Une fois défini le matériau plus adapté au programme et aux problématiques constructives de notre navire, il faut "organiser" le maillage structurel, et calculer les épaisseurs, hauteurs des différents éléments prenant part à cette structure.
De manière générale, quel que soit le matériau utilisé, les structures sont organisées comme suit :
- les éléments longitudinaux principaux sont nommés carlingues lorsqu'ils sont à fond de coque, et élongis lorsqu'ils soutiennent le pont. Sur les bateaux en charpente bois traditionnelle, l'élément longitudinal principal est avant tout la quille, sur laquelle viennent se greffer tout les autres éléments.
- les éléments longitudinaux secondaires sont nommés serres, lorsqu'ils se trouvent au livet (serre bauquière), ou au bouchain. On peut nommer également lisses les petits raidisseurs longitudinaux servant principalement à rigidifier un bordé.
- les éléments transversaux sont eux nommés en partant du plus bas au plus haut : varangue dans les fonds, membrure du fond jusqu'au livet, puis barrot soutenant le pont.
- les cloisons désignent bien évidement les éléments structurels 'pleins', dans lesquels sont ménagés ou non des ouvertures
- lorsqu'une structure transversale forme un anneau complet, et de dimensionnement plus important que la structure générale du bateau, il est nommé porque. Cela sert souvent à diffuser des efforts de compression, sans pour autant devoir ajouter une épontille (pilier vertical) qui diviserait l'espace.
Afin de dimensionner tout nos éléments de structure, il faudra lister l'ensemble des efforts auxquels sera soumis notre navire, puis calculer un échantillonnage en fonction.
Un bordé de coque, par exemple, sera considéré comme une plaque bombée, en appui sur des éléments de structure longitudinaux et transversaux. Cette plaque devra pouvoir résister à la pression de l'eau non seulement en statique, mais aussi en dynamique lorsque le navire fera route. Le bordé sera donc dimensionné en flexion essentiellement.
Pour un raidisseur vertical (épontille), ce sera majoritairement la compression qui déterminera sa section, voire le flambement, si l'élément est assez long.
Une membrure travaillera en flexion. Assimilée à une poutre, un peu courbée certes, il faudra distinguer plusieurs contraintes différentes : sur la face intérieure de la traction, sur la face extérieure de la compression, et entre les deux (l'âme du raidisseur, à ne pas confondre avec l'âme du sandwich), du cisaillement
Une cadène, quand à elle travaillera principalement en traction.
Un peu de lecture pour approfondir tout ceci ?
En plus des ouvrages généraux d'architecture navale, cités dans le second post de ce blog, vous pouvez vous plonger dans la passionnante lecture de Composite Materials, de D.Gay (in english only !), et éplucher les brochures des fabricants de profilés acier et aluminium pour la construction navale.
Au prochaine épisode, il sera question de stabilité, car pour exploiter au mieux notre belle carène, maintenant si solide et si légère, mieux vaut qu'elle reste dans le bon sens !