Peut-on se fier à l’accastillage inox ?
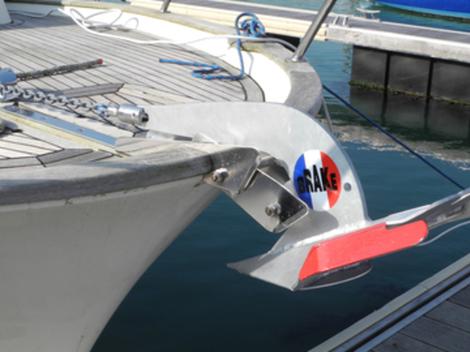
Pour beaucoup l’inox est le matériau idéal sur un bateau. Il ne rouille pas, est résistant et vieillit bien dans le temps. Ces affirmations peuvent être vraies mais sous certaines conditions.
Tous les inox ne se valent pas
Dans un milieu agressif comme la mer, les plus répandus sont le 18-10 (norme US 304 L), 18-12 MO (316 L), 18-10 CU (305 CU) et le 17-4 PH (630). Contrairement aux idées reçues, un inox n’est pas nécessairement amagnétique et insensible à la corrosion (inoxydable). En effet, ces deux qualités sont liées à sa composition et, en particulier, à la teneur en carbone. Pour augmenter la résistance, la solution retenue est l’ajout de carbone. Ce dopage confère à l’acier une résistance de l’ordre de 75% supérieure à un acier inox 18-12 MO. En contrepartie, la présence de carbone rend le matériau plus corrosif et légèrement magnétique. Pour minimiser ces deux effets, les métallurgistes introduisent dans sa composition du cuivre, du cobalt, du nobium et du tantale. Ces pièces ainsi réalisées sont estampillées HR (haute résistance).
La fabrication
Deux techniques sont employées pour la fabrication surtout pour les manilles et mousquetons : le moulage (microfusion) et le forgeage.
Pour le moulage, le métal est chauffé pour le mettre en fusion puis il est coulé dans un moule ayant la forme de la pièce à réaliser. L’ébauche ainsi obtenue sera ensuite usinée pour avoir son aspect final.
Le forgeage, technique plus ancienne, comporte deux phases : le corroyage et l’estampage. Le corroyage consiste à compresser un lingot de métal pour en diminuer la section. Une fois cette première opération accomplie, le métal est chauffé et mis en pression entre deux matrices portant en creux la forme de la pièce à obtenir (opération d’estampage). Les matrices possèdent des gravures qui permettent d’orienter les fibres du métal en fonction des contraintes que la pièce finale devra subir.
Les deux techniques ont leurs avantages et leurs inconvénients. Une pièce moulée est plus économique à réaliser qu’une pièce forgée. A l’utilisation, son pouvoir élastique est pratiquement nul. Au-delà d’une certaine force (rupture), elle casse sans prévenir. La qualité de la pièce fabriquée est liée à la pureté du métal et à son homogénéité en fusion. S’il n’est pas parfaitement homogène des micros criques internes peuvent se former et affaiblir la résistance de la pièce.
Sur une pièce forgée, il y a peu de risque d’irrégularité dans la structure. A l’usage, avant rupture, il y a allongement et déformation. Mais, attention, une pièce forgée qui a été déformée sous un effort important (au-delà de la rupture annoncée par le constructeur), peut retrouver sa forme d’origine, fonctionner correctement mais présenter des lésions internes qui peuvent la rendre plus fragile.
Jouez la sécurité
Il existe sur le marché d’excellents produits moulés et forgés mais, attention, on en trouve de plus en plus de mauvaise qualité spécialement en acier moulé.
Pour preuve, la photo que nous vous donnons est celle d’un émerillon de 18 mm conçu pour un mouillage. Si une telle pièce est fabriquée dans les règles, elle a une charge de rupture de 18.000 kg et une de travail voisine de 7500 kg. Celle que nous présentons, a cassé simplement en dévissant son axe ! Et, comme on peut le voir la structure interne était poreuse.
La qualité a un prix, pour les équipements liés à la sécurité (mousqueton de harnais, mouillage, haubanage, etc.), n’hésitez pas, prenez des produits de qualité. Pour les reconnaître ce n’est pas évident s’ils ne possèdent pas de signes extérieurs ni de référence à un catalogue. Là, vous pouvez tomber sur des produits de mauvaise qualité qui ne devraient pas être proposés par les accastilleurs.
La solution, fiez-vous à la marque gravée sur la pièce (Wichard, Harken, Lewmar, Gibb, Tylaska, etc.), c’est un signe de sérieux qui engage le fabricant. Ce dernier donne en plus dans les catalogues la charge de rupture et de travail.