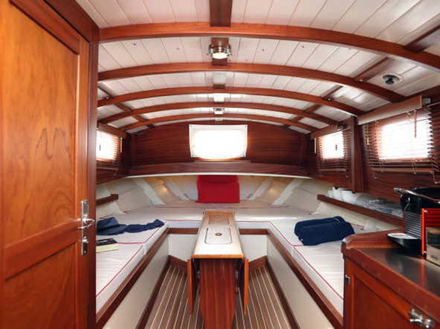
Entre hausse vertigineuse des cours du pétrole et impact écologique à minorer, le si économique composite polyester voit certaines certitudes s’effondrer. Historiquement, ses composants, des fibres de verre et de la résine polyester dont il tire son nom, sont d’un très bon rapport prix / propriétés de résistance. Qui plus est, sa mise en œuvre en moule femelle est parfaitement adaptée à une production en série : temps de production optimisés, qualité du composite réalisé sous vide (infusion) et excellent niveau de finition, l’ensemble étant duplicable à souhait. Certes l’investissement de départ en outillage est important, mais plus il en sortira de bateaux, mieux il sera amorti, c’est la loi de l’industrie.
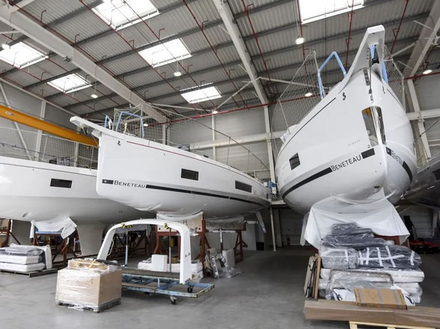
Au royaume du polyester
Ce matériau brut, ou plus exactement monolithique, sous l’influence de la course au large notamment, a évolué pour devenir ‘sandwich’. En insérant une ‘âme’, on améliore le ratio poids / résistance du composite. Cette âme, selon la zone d’utilisation, peut être constituée de balsa, de contre-plaqué, de feutre ou de mousse. Si le bois est de moins en moins courant, ses qualités de résistance à la pression ou au cisaillement restent pourtant appréciées dans des endroits très sollicités comme le pied de mât, les pieds de winches, ou autour des axes de barres à roue. Lorsque le programme se veut œcuménique, un mix est proposé entre œuvres vives en monolithique extrêmement résistantes au poinçonnement (échouage, chocs…) et œuvres mortes au-dessus de la flottaison en sandwich pour alléger au maximum.
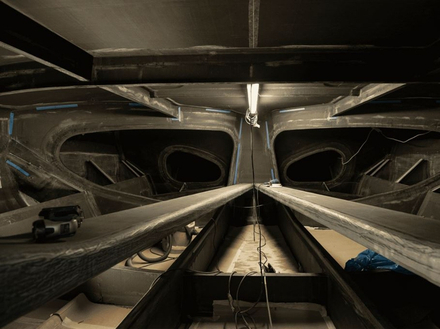
Sandwich à la carte
Mais cette âme ne serait rien sans une structure susceptible de résister aux efforts énormes que subissent nos bateaux, à voile ou à moteur. La fibre de verre se taille en la matière une large part de marché, toujours pour des raisons économiques. Selon les zones, sa présentation et son poids au mètre carré, varient pour s’adapter le plus précisément possible aux contraintes. Sur les bateaux les plus performants, elle peut être remplacée par de la fibre carbone dont la résistance est de 70% à 140% supérieure à poids. En version ‘haut module’ la fibre de carbone, le niveau de performance est même de 400 à 500% plus élevé. A résistance égale, le gain se fait alors sur le poids, dans le même ordre de grandeur. Beaucoup moins flexible le carbone apporte une raideur favorisant la performance. Mais cela pénalise aussi le confort, car aucun bruit n’est amorti. D’où l’usage de renforts carbone localisés, seulement là où les efforts sont les plus importants.
Le roi epoxy
Enfin, dernier élément constitutif du composite, la résine fait le liant entre les fibres et l’âme. La résine polyester, a même fini par donner son nom au matériau pourtant composite. Sensible à l’osmose, phénomène qui a défrayé les chroniques nautiques à la fin du siècle dernier, elle est de désormais souvent remplacée par du vinylester, ou de la résine epoxy, insensibles à ce phénomène. Cette dernière offre de meilleures performances physiques mais requiert une mise en œuvre (température, hygrométrie…) plus soignée.
L’alu pour voyager loin
Derrière la très vaste industrie du ‘plastique’, quelques constructeurs continuent sur des chemins différents qui offrent d’autres avantages. Matériaux très résistant, l’aluminium a une capacité de déformation sous l’effet de chocs, qui séduit les navigateurs au long cours. Son ratio poids-résistance est très intéressant, et on peut faire varier son épaisseur selon les zones. Surdimensionnées dans les fonds, les tôles peuvent passer de 12mm dans les fonds à 6mm sur les bancs de cockpit, optimisant ainsi le devis de poids. Ne nécessitant pas de moules, l’investissement de départ est réduit, mais demande en contrepartie plus d’heures de travail et un vrai savoir-faire pour obtenir un rendu de coque au rendu parfait.
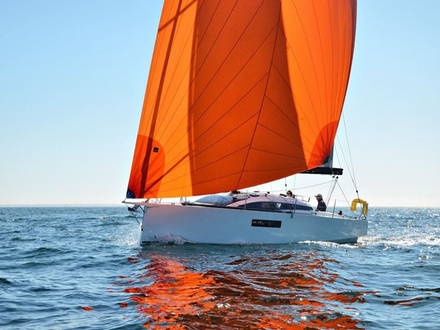
Le bois n’a pas dit son dernier mot
Enfin, mais nous aurions pu écrire aussi, à l’origine, il y a le bois. Une technique de production onéreuse, reprise pourtant parfois en petite série à l’image des fameux RM. Leurs lignes tendues et à bouchains sont liées à leur mode de construction en CP-epoxy. Facilité de travail du bois, rigidité des collages epoxy, finitions intérieures laquées faciles à entretenir c’est le trio gagnant de ce mode constructif. Plus rustique encore sont les fameux plans Wharram, dont la simplicité des plans et des matériaux a le bon goût de permettre encore à un constructeur amateur de partir sur un bateau réalisé de ses mains.
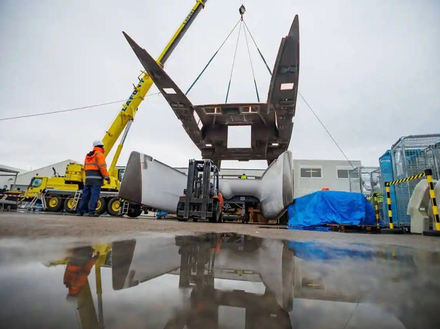
Construire propre, naviguer sain, recycler bien
Alors que la problématique de la déconstruction des premiers bateaux en polyester produits par l’industrialisation de la plaisance se fait de plus en plus prégnant, l’avenir de nos bateaux sera écologique ou ne sera pas. Fibre de bambou, fibre de lin, bâches d’infusion réutilisables… de nombreuses évolutions sont en cours et ne devraient pas manquer de se diffuser de plus en plus largement. Car les alternatives, bois ou aluminium, qui ont entre autres avantages, celui d’être quelque part ‘recyclables’, ne peuvent, économiquement parlant, que concerner de la petite série. Mais ils continueront de faire le bonheur de constructeurs amateurs éclairés pour le premier, des bateaux de grande croisière bien sécurisées et des grandes unités sur mesure pour le second.
POIDS DE DIFFÉRENTS BORDÉS A RÉSISTANCE ÉGALE
> Polyester monolithique : 13,5 kg/m2
> Sandwich mousse-verre : 9,1 kg/m2
> Sandwich mousse carbone : 3,6 kg/ m2
> Lamellé collé Red Cedar : 10,9 kg
> Contreplaqué : 11,75 kg
> Aluminium : 13,7 kg
Source : Matériaux composites, Editions Loisirs Nautiques, Erik Lerouge.